基于PLC技术的焊接机器人主从协调运动控制系统研究
2023,31(7):122-127
摘要:焊接机器人运动控制系统的控制功能直接决定了焊接工作质量,利用PLC技术优化设计焊接机器人主从协调运动控制系统。在系统硬件设计方面,装设位置、速度、旋转电弧等传感器设备,利用传感数据检测焊接机器人实时位姿。在考虑焊接机器人组成结构、工作原理以及动力驱动方式的情况下,构建焊接机器人的数学模型。结合当前位姿和控制目标之间的位置关系,规划焊接机器人主从协调运动轨迹,在约束条件的作用下,利用PLC控制器生成控制指令,作用在改装的焊接机器人驱动器上,实现系统的焊接机器人主从协调运动控制功能。通过系统测试实验得出结论:与传统控制系统相比,优化设计系统的速度控制误差、姿态角控制误差分别降低了0.075mm/s和0.38°,在优化系统控制下,主从焊接机器人的运动轨迹与规划轨迹之间无明显差异。
关键词:PLC技术;焊接机器人;主从协调运动;运动控制系统;
Research on master-slave coordinated motion control system of welding robot based on PLC Technology
Abstract:The control function of welding robot motion control system directly determines the quality of welding work. PLC technology is used to optimize the master-slave coordination motion control system of welding robot. In terms of system hardware design, sensor devices such as position, velocity and rotating arc are installed to detect the real-time pose of the welding robot using sensor data. Considering the structure, working principle and dynamic driving mode of welding robot, the mathematical model of welding robot was constructed. Combined with the position relationship between the current pose and the control target, the master-slave coordinated motion trajectory of the welding robot was planned. Under the action of constraints, the PLC controller was used to generate control instructions, which acted on the modified welding robot driver and realized the master-slave coordinated motion control function of the system. Through the system test experiment, it is concluded that compared with the traditional control system, the speed control error and attitude Angle control error of the optimized design system are reduced by 0.075mm/s and 0.38°, respectively. Under the control of the optimized system, there is no significant difference between the motion trajectory and the planned trajectory of the master-slave welding robot.
Key words:PLC technology; Welding robot; Master-slave coordinated movement; Motion control system;
收稿日期:2022-09-01
基金项目:
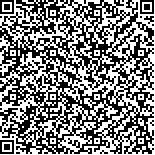